Norwalk City Hall
(1998-2006)
Building-wide Energy Management System (EMS) with Variable Air Volume & Variable Frequency Drives (VAV/VFDs), enthalpy and CO2 Demand Control Ventilation (DCV).
- Total building floor area 198,000 square feet (including 40,000 square foot concert hall)
- Total building annual electrical consumption: 2,140,000 KWH/yr (before Retrofit)
- Total annual electrical energy (cost) savings @ 14%: 299,600 KWH ($28,000.00 @ 9.36¢/KWH)
- Total building annual natural gas consumption: 48,800 CCF/yr
- Total annual natural gas energy (cost) savings @ 19%: 9,300 CCF ($5,600.00 @ 60¢/CCF)
- Retrofit Energy Conservation Measures (ECM) cost (5 phases) $180,000.00
- Simple payback (Return On Investment) 64 months (19%)
- Simple payback (Return On Investment) 50 months (24%) including total CL&P Incentive Awards @ $40,000.00
- US EPA Energy Star Benchmark: 69% (Prior to Retrofit) vs. 80% (after ECM/EMS Retrofit)
- NOTE: The US EPA Benchmarking "Portfolio Manager" scores buildings between 0 and 100% efficiency with 75% being the minimum required score for "distinction"
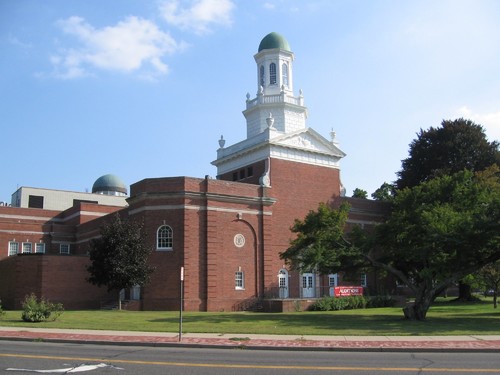
TRI TOWN PRECISION PLASTICS (2008-2009)
Process control with hydraulic pump motor optimization.
- Total building annual electrical consumption 3,159,200 KWH (before retrofit)
- Annual energy (cost) savings @ 11.2% 353,800 KWH ($48,600.00 @ 13.75¢/KWH)
- Retrofit Energy Conservation Measures (ECM) cost $97,200.00
- Simple payback (Return On Investment) 24 months (50% ROI) without CL&P Incentive Award
- Simple payback (Return On Investment) 12 months (100% ROI) including CL&P Incentive Award @ $48,500.00
NOTE: This pilot project for industrial motor optimization was the first customized process control of this type funded by CL&P within the state of Connecticut.
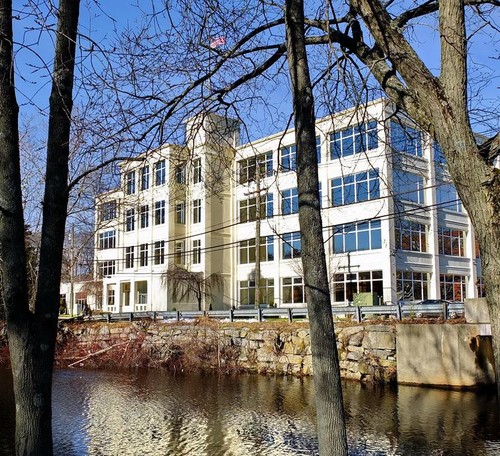
GREENWICH CAPITAL/RBS CORP. CTR.
(2000-2003)
Building-wide Energy Management System (EMS) installation and AHU/AC controls.
- Total building floor area: 275,000 square feet
- Total building annual HVAC electrical consumption: 5,284,000 KWH/yr (before retrofit)
- Annual energy (cost) savings @ 5.5%: 293,000 KWH ($28,000.00 @ 9.56¢/KWH)
- Total Energy Conservation Measures (ECM) cost: $120,000.00 (multiple phases)
- Simple payback (Return On Investment): 51 months (23%) without CL&P Incentive Award
- Simple payback (Return On Investment): 29 months (40%) including CL&P Incentive Award @ $51,600.00
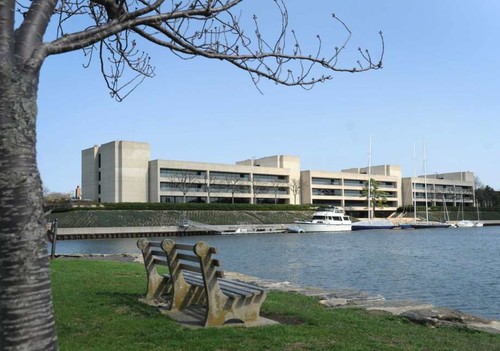
CANTERBURY ELEMENTARY SCHOOL
(2010-2011)
Building-wide Energy Management System (EMS) installation and Exterior Building, Lumen-Based Lighting Controls
- Total building floor area: 45,000 square feet
- Total building annual electrical consumption: 341,100 KWH/yr (before retrofit)
- Total building annual #2 Fuel Oil consumption: 17,100 gallons (before retrofit)
- Total cost of Energy Conservation Measures (ECM's) proposed: $111,643.00 including NEMA premium efficiency motors EMS with Demand Control Ventilation (DCV), Refrigeration EC Motor/Smart Defrost Controls and exterior lighting retrofit with the newest induction fixtures.
- Total CL&P "Comprehensive" project (*option #1) incentives at $45,359
- Total project (option #1) 26% Electrical savings 88,870 KWH ($10,828.71)
- Total project (option #1) 34% No. 2 Fuel Oil Savings: 5,816 Gallons ($14,209.00)
- Customers ARRA (P.L 111-5) "stimulus" Grant @ $34,249.00
- Project (option #1) Net annual capital cost = ($111,643 - 104,645.71) = $6,997.29 (with both estimated annual energy cost savings and utility incentives)
- Project (option #1) Simple payback (Return On Investment): 53 months (22.4%) without ARRA or CL&P Incentives
- Project (option #1) Simple payback (Return On Investment): 32 months (38.5%) with CL&P Incentives Only
- Project (option #1) Simple Payback (Return On Investment): 15 months (78.7%) with both ARRA and CL&P Incentives
*NOTES:
1. This client eventually opted for smaller scale project (Option #2) with a total cost of $55,939.90 (consisting of EMS and exterior building Lumen-based lighting controls only) that when factoring the ARRA stimulus ($34,239) and reduced CL&P incentive ($21,690.90) required zero capital outlay and will generate 52,006 KWH ($9,881.00) in Electrical savings and 5,816 gallons of No 2 Fuel Oil ($14,209.00) during the first year after installation.
2. "Comprehensive" refers to CL&P incentives which are increased by an additional bonus of 10% for projects packaged with both lighting and non-lighting Energy Conservation Measures.
3. The above project (option #1) would have more than doubled USA/EPA benchmark equivalent at 31% for this building to over 62%. The client finally selected downscaled-project (option #2) will still raise the USA/EPA benchmark from currently at 31% to over 50% which is the national average for school buildings. "Benchmarking" scores buildings between 0 and 100% efficiency with 75% being the minimum required target score for "Energy Star Distinction"
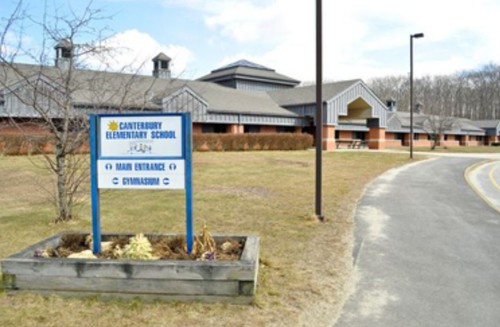
CROMWELL MIDDLE SCHOOL
(1996-2011)
Building-wide Energy Management System (EMS) Refrigeration EC Motor / Smart Defrost Controls and Exterior Lighting Retrofit with Newest Induction Fixtures and Interior Lighting Occupancy and Lumen-based Sensors
- Total building floor area: 92,600 square feet
- Total building annual Electrical consumption: 418,000 KWH/yr (before Phase II Retrofit)
- Total building equivalent natural gas consumption: 57,065 CCF (before Phase II Retrofit)
- Total cost of Phase II Energy Conservation Measures: $122,174.68 (Including EMS with Demand Control Ventilation (DCV), Steam Trap Replacement, NEMA Premium Efficiency Motors, Exterior Lighting Retofit with Induction Fixtures and Interior Lighting Occupancy and Lumen-based sensor controls)
- Total CL&P "Comprehensive" Project* Incentives @ $53,234.50
- Total Project 14.2% Electricity Savings: 59,266 KWH ($10,312.27)
- Total Project 22.7% CCF Natural Gas Savings: 12,956 ($14,898)
- Total Net Annual Capital Cost = ($122,174.68 - $78,444.27) = $43,730.41 (with both 1st year annual energy cost savings and utility incentives)
- Project Simple Payback (Return On Investment): 57 months (20.7%) without CL&P Incentives
- Project Simple Payback (Return On Investment): 32 months (33.6%) without CL&P Incentives
*NOTES:
1. The above energy economic analysis is for this clients implementation
of Phase II Energy Conservation Measures. Prior to Phase II, over the past 10 years, annual energy consumption levels were reduced by over 15% by implementation of Phase I Energy Conservation Measures including: EMS (boiler staging and time of day building occupancy temperature controls), and a partial interior lighting fixture retrofit project.
2. "Comprehensive" refers to CL&P incentives which are increased by a bonus of 10% for projects with both lighting and non-lighting energy conservation measures.
3. This client received and completed a separately contracted $1,036,000 roof mounted photovoltaic panel project partially funded @ $513,400 through the CT Clean Energy Fund/Grant that was contingent on concurrent implementation of the above Energy Conservation Measures in an attempt to raise the current "US/EPA Benchmarking" Scores from current levels (between 56% and 61%) to 75%; "Benchmarking" Scores buildings between 0 and 100% efficiency with 75% being the minimum required target score for "Energy Star" Distinction. The solar Photo Voltaic (PV) project is projected to produce 209,500 KWH/yr (or approx $36,450/year) while the ECM projects shown above with CL&P incentives will save an additional 59,266 KWH/year (or $10,312.27) in electricity and 12,956 CCF/year ($14,898) in natural gas consumption. In terms of Measurement and Verification (M&V) the two separate projects (i.e. generation of electricity and metering for building consumption and conservation) will be integrated through the web-based internet functions of NEEC's KMC/KM Digital Energy Management System (EMS).
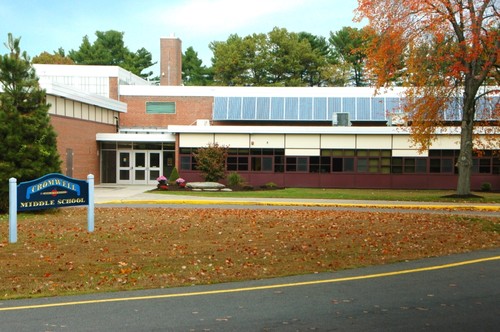
CROMWELL EDNA C. STEVENS SCHOOL
(1996-2011)
Building-wide Energy Management System (EMS) Refrigeration EC Motor/Smart Defrost Controls and Exterior Lighting Retrofit with Newest Induction Fixtures and Interior Lighting Occupancy and Lumen-based Sensors
- Total building floor: 67,800 square feet
- Total building annual electrical consumption: 295,000 KWH/yr (before Phase II Retrofit)
- Total building annual No. 2 Fuel Oil Consumption: 26,000 Gallons (before Phase II Retrofit)
- Total cost of Phase II* Energy Conservation Measures: $84,275.95
- (Including EMS, NEMA Premium Efficiency Motors Demand Control Ventilation (DCV), Exterior Lighting Retrofit with Induction Fixtures and Interior Lighting Occupancy and Lumen-based sensor controls.)
- Total CL&P "Comprehensive" project* incentives @ $33,734.50
- Total Project 18.6% Electricity Savings: 54,839 KWH ($9,278.71)
- Total Project 13.2% No. 2 Fuel Oil Savings: 3,429 Gallons ($8,229)
- Total Net Annual Capital Cost = ($84,275.95 - $51,242.21) = $33,033.74 (with both 1st year annual energy cost savings and utility incentives)
- Project simple payback (Return On Investment): 57 months (20.8%) without CL&P Incentives
- Project simple payback (Return On Investment) 34 months (34.5%) with CL&P Incentives
*NOTES:
1. The above energy economic analysis is for this client's implementation
of Phase II Energy Conservation Measures. Prior to Phase II, over the past 10 years annual energy consumption levels were reduced by over 15% by implementation of Phase I Energy conservation Measures including: EMS (boiler and time-of-day building occupancy automatic temperature controls) and a partial interior lighting fixture retrofit project.
2. "Comprehensive" refers to CL&P incentives which are increased as a bonus of 10% for projects with both lighting and non-lighting energy conseravation measures.
3. This client received and completed a separately contracted $677,400 roof-mounted photovoltaic panel project partially funded @ $336,000 through the CT Clean Energy Fund/Grant that was contingent on concurrent implementation of the above Energy Conservation Measures in an effort to raise the current "US/EPA Benchmarking" scores from current levels (between 67% and 70%) to 75%; "Benchmarking" scores buildings between 0 and 100% efficiency with 75% being the minimum required target score for "Energy Star Distinction". The solar Photo Voltaic (PV) project is projected to produce 131,600 KWH/year (or approx. $22,900/year) while the ECM projects shown above with CL&P incentives will save an additional 54,839 KWH/year ($9,278.71) in electricity. In terms of Measurement and Verification (M&V), the two separate projects (i.e. generation of electricity and metering for building consumption) will be integrated through the web-based internet functions of NEEC's KMC/KM Digital Energy Management System (EMS).
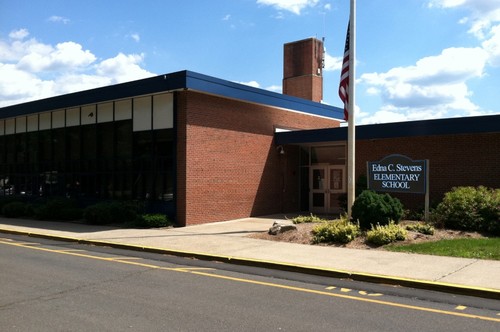
CROMWELL WOODSIDE INTERMEDIATE SCHOOL
(2005-2010)
Building-wide Energy Management System (EMS) and Interior and Exterior Lumen-based sensor lighting controls and interior lighting occupancy sensors
- Total building floor: 86,055 square feet
- Total building annual electrical consumption: 785,000 KWH/yr
- Total building fossil fuels: 57,000 CCF (Natural Gas) & 10,000 Gals (No. 2 Fuel Oil)
- Total Phase II* CL&P Incentives @ $10,000
- Total Project 14.5% Electricity Savings: 113,540 KWH/yr ($22,224)
- Total Net Annual Capital Cost = ($22,564.89 - $32,224) = -$9,659.11 (with both 1st year annual energy cost savings and utility incentives)
- Project simple payback (Return-On-Investment): 1 month (125%) without CL&P incentives
- Project simple payback (Return-on-Investment): < 1 month with CL&P incentives
*NOTES:
1. The above energy economic analysis is for this client's implementation of Phase II Energy Conservation Measures. Prior to Phase II, this new building was initially completed as a 2005-2006 $20 Million Project under Turner Construction Managers that included a $300,000 EMS (Phase I)
2. This Energy Conservation measure illustrates that even within a relatively new building of less than 5 years old with energy efficient designs, a properly targeted and engineered strategy which in this case included lumen-based exterior lighting (or "night harvesting") and interior lighting (or "daylight harvesting") generated (with the zero net capital cost as shown above) a $9,659.11 in positive cash flow in the 1st year after installation. "Day-light harvesting" includes sophisticated EMS control including turning off segregated zones of all building vestibule entrances (total quantity = 5; note: see typical vestibule tower shown in picture to the right), multipurpose/cafeteria and Library perimeter interior lighting zones each by utilizing natural sunlight window exposures detected through multiple EMS room mounted lumen (variable foot candle) setpoint sensors. "Night harvesting" includes sequentially turning off some of the seven (7) exterior building lighting zones at different times of the night, rather than running them from dusk to dawn on a simple photocell.
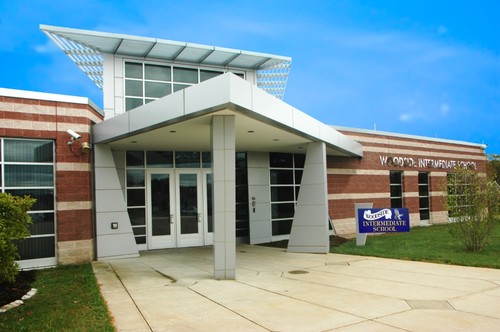